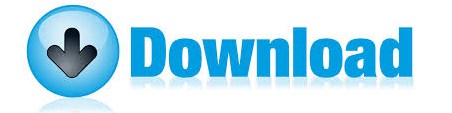
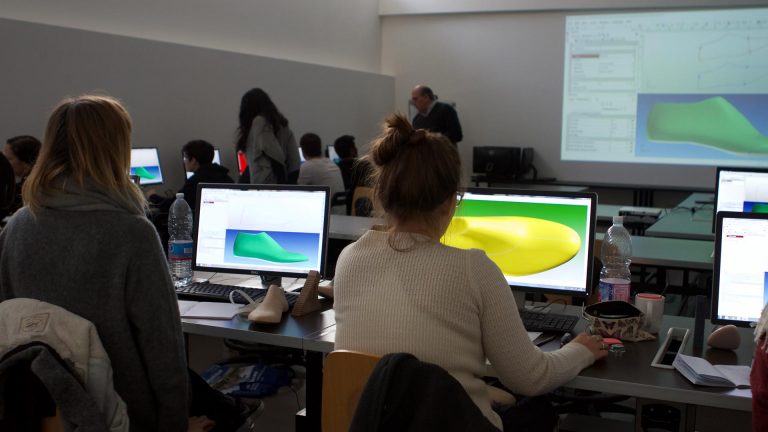
“Material waste has been drastically reduced, and we've eliminated the chemical fillers we used for sculpting new shapes.” Hand crafting meets digital “We can now visualize a last before it is used to make a shoe, and if needed, create a rapid physical prototype within three-to-four hours for a design and engineering review,” says Anderson.
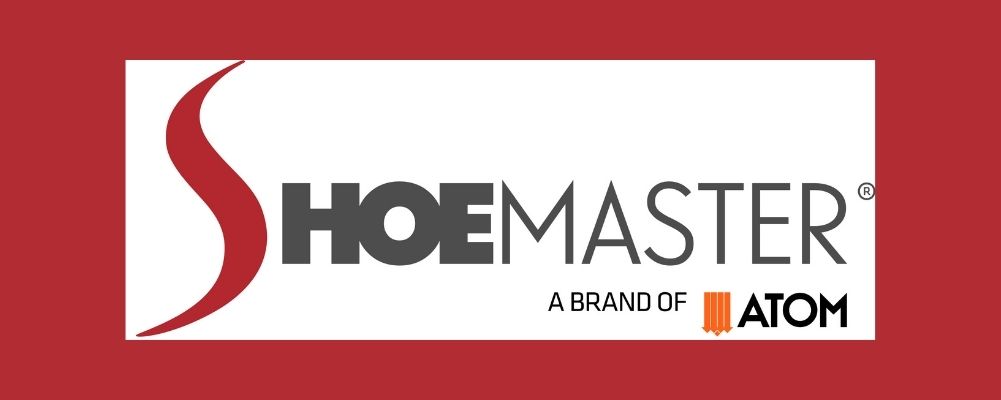
As a result of using 3D reverse engineering, reworks, a frequent occurrence with hand-made lasts, have been reduced by 75 percent, according to Terry Anderson, a Timberland Last engineer. With the new 3D process in place, hand-made lasts now represent only 10 percent of lasts used for design and manufacturing. Incorrect and outdated lasts were thrown away, unless they were newer ones made with polypropylene, which can be recycled. Until two years ago, all lasts were created and modified by hand, then shipped to the company's manufacturing facility in the Dominican Republic, or to Asian partners in Thailand, Vietnam and China. Timberland currently produces between 100 and 120 lasts per year across its major product lines: Outdoor Performance, Authentic Youth, Industrial-PRO, and Casual Gear. Traditionally these were made of wood, but now they are generally made from blocks of plastic milled by CNC machines. Since ancient times, shoes have been designed and made according to lasts, a mold that approximates the form of the human foot within various styles of shoes. The Block Island model debuted in Canada and North America in December 2006, followed by Europe in February 2007 and Asia in April 2007. Pictures of Timberland's Block Island shoe manufactured from the digital shoe last shown in the other images. It might not be the stuff that inspires rappers' rhymes, but it could well mark a turning point in how shoes are designed and manufactured in a global enterprise, to a worldwide customer base. The latest innovation salvo from the nearly 90-year-old company is taking place behind the scenes: Timberland is using 3D reverse engineering technology from Geomagic for greater footwear customization, faster time to market, more consistent quality, and manufacturing with considerably less waste.
FOOTWEAR DESIGN SOFTWARE FOR MAC FULL
Over the last decade, the Timberland product line has expanded from rough-and-ready outdoor boots to a full line of footwear and apparel for men, women and children. The result: one of the first truly waterproof boots. In the 1960s, the company introduced injection-molding to the footwear industry, fusing soles to leather uppers without stitching. On the corporate side, Timberland's commitment to social responsibility is respected and emulated worldwide.Īmid all this, it's easy to forget that Timberland is also a manufacturing innovator. The nickname “Timbs” is name-checked on dozens of hip-hop lyrics, and one of the genre's best-selling producers, Timbaland, is named after the company's footwear. As well, we are not responsible for the loss or damage of return shipments, so we suggest that you package your return shipment protectively and send by registered mail or courier.Timberland is a cultural icon, a dream brand.
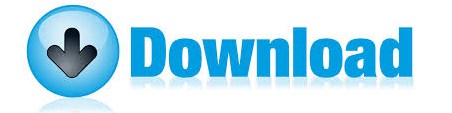